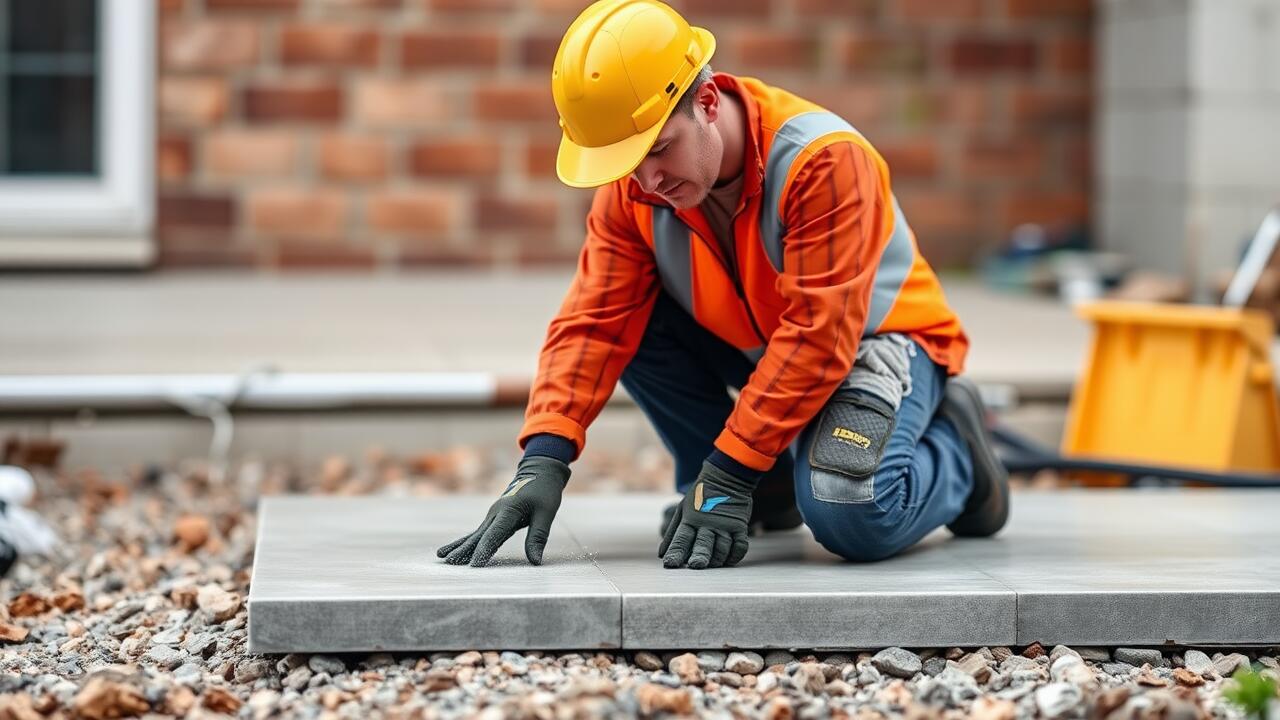
Regional Variations in Concrete Pricing
Concrete pricing can fluctuate significantly based on geographic regions, with urban areas generally commanding higher costs than rural locations. Factors such as local demand, availability of raw materials, and transportation costs contribute to these disparities. In places where concrete contractors are plentiful, competitive pricing may prevail, while in less populated regions, fewer providers could lead to inflated rates. Seasonal variations may also play a role, affecting when projects are scheduled and influencing overall pricing.
For instance, Concrete Slab Installation in Central City, Phoenix, may reflect higher price tags due to the confluence of demand and specific climate considerations. The extreme heat in Phoenix can impact the curing process, requiring contractors to implement specific techniques that may further raise labor costs. Additionally, the concrete mix utilized could vary based on regional standards and practices, affecting overall expenses for a project. Local building codes can also dictate specific requirements that might necessitate additional materials or labor, ultimately adding to the project's budget.
How Location Impacts Material and Labor Costs
The cost of concrete slab installation varies significantly based on geographic location, influenced by regional market conditions. Areas with higher demand for concrete and construction services often experience increased prices for both materials and labor. For instance, in regions with dense urban populations, supply chains may be strained, driving up costs. In contrast, rural areas may have lower prices due to less competition and potentially lower labor costs.
In Central City, Phoenix, factors such as local climate, availability of resources, and the overall cost of living play crucial roles in determining pricing. The hotter climate may require specific mixes or techniques to ensure durability, affecting material expenses. Labor costs can also vary, as skilled workers might command higher wages in areas with a booming construction market. Understanding these local factors can help homeowners and contractors accurately estimate the total cost of a concrete slab installation project.
DIY vs. Hiring Professionals
Choosing to tackle concrete slab installation as a DIY project can save on labor costs. Homeowners can purchase the necessary materials and rent equipment, such as mixers and forms, minimizing expenses related to hiring professionals. However, this path requires a solid understanding of the process. If not executed correctly, the risk for errors can lead to increased costs through materials wasted or the need for repairs later.
On the other hand, hiring professionals for concrete slab installation in Central City, Phoenix, comes with its own set of benefits. Experienced contractors possess the expertise to ensure a smooth and efficient installation. They are familiar with local regulations and can handle permits and inspections, reducing the risk of compliance issues. While this option is generally more expensive upfront, the investment often results in higher quality and durability that can save money in the long run.
Cost Comparison of Do-It-Yourself Projects
For many homeowners, taking on a DIY project for pouring a concrete slab can appear to offer significant savings. The primary costs involved will include purchasing materials such as concrete mix, gravel, and reinforcements, along with necessary tools for mixing and pouring the concrete. Concrete Slab Installation in Central City, Phoenix, may necessitate additional attention to detail, ensuring the slab meets local standards. Despite the initial savings on labor costs, this approach demands a considerable investment of time and effort.
On the other hand, while hiring professionals may seem more expensive upfront, their expertise can alleviate risks associated with improper installation. They provide not only the manpower but also experience in managing site preparation, mixing proportions, and achieving optimal curing times. In areas like Central City, Phoenix, the logistical challenges of access and material delivery can also shift costs upward for DIY projects, making professional assistance a more appealing option for some homeowners.
Hidden Costs to Anticipate
When planning a concrete slab project, homeowners often overlook several hidden costs that can arise during the process. For instance, if you're considering a large-scale endeavor like a concrete slab installation in Central City, Phoenix, it's essential to factor in costs for permits and inspections that may be required by local regulations. These fees can vary significantly depending on the area and the project's size. Additionally, the terrain and accessibility of the site can influence expenses, as any necessary grading or preparation work adds to the overall bill.
Another often-ignored expense is the potential for unexpected repairs that might be needed before or after the installation. Soil quality can affect the stability of the slab, which may necessitate additional measures such as reinforcing materials or drainage solutions. Furthermore, costs associated with managing waste or obtaining specific tools for the job can also impact your budget. By thoroughly researching and accounting for these hidden costs upfront, you can ensure that your project remains on track and within financial limits.
Permits and Inspections
Before commencing any concrete slab project, it's crucial to check local regulations regarding permits and inspections. Most municipalities require homeowners to secure a permit for work on concrete slabs, including those for patios, sidewalks, or driveways. These permits ensure that the construction meets safety and building codes. In the case of Concrete Slab Installation in Central City, Phoenix, for instance, specific guidelines may dictate setbacks, minimum thickness, and reinforcement requirements.
Inspections may also be necessary at various stages of the project. A building inspector may review the site before pouring the concrete to ensure the foundation complies with zoning laws and safety standards. Failing to obtain the required permits or passing inspections can lead to fines and even the necessity of removing the structure altogether. It's wise to factor these potential costs and the time required for approvals into the overall budget for the concrete slab project.
FAQS
What is the average cost to pour a 30x30 concrete slab?
The average cost to pour a 30x30 concrete slab typically ranges from $3,600 to $5,400, depending on factors like location, material quality, and labor costs.
How do regional variations affect concrete pricing?
Regional variations can significantly impact concrete pricing due to differences in local demand, transportation costs, and the availability of materials and skilled labor.
Is it cheaper to do it myself or hire professionals for pouring a concrete slab?
While DIY projects may save on labor costs, they can end up being more expensive due to potential mistakes, the need for specialized equipment, and the time investment required. Hiring professionals often ensures better quality and efficiency.
What hidden costs should I anticipate when pouring a concrete slab?
Hidden costs can include permits and inspections, site preparation, reinforcements, finishing touches, and potential repairs if issues arise during the pouring process.
Do I need a permit to pour a concrete slab?
In many areas, a permit is required for pouring a concrete slab, especially if it is part of a larger construction project. It's essential to check with local building authorities for specific regulations.